Our main objective this month was to complete our final design choices and prepare purchases for immediate machining/installment.
Starting out, the team focused on finalizing our choices for the main ramp components—namely, the expanded metal flooring, handrails, and ramp hinge(s).
For the expanded metal flooring, we considered McMaster items that heavily reflected the preferences laid out by previous teams. These preferences include a carbon steel composition of the expanded panel, a raised panel style, openings of 2.5″ width and 1.19″ length, and overall sizes that satisfy the top dimensions of the platform and ramps. Thus, three McMaster 9302T66 Carbon Steel Expanded Panels were selected for purchase.
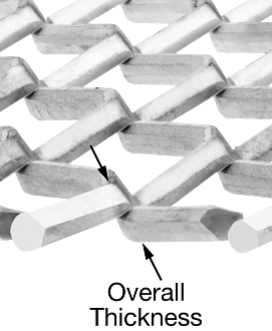
Considering that a detachable handrail is preferred for the mounting ramp, a Uline 6′ Steel Safety Handrail was selected due to it having circular slot ends for sockets and an overall length that is within the length-wise [Insert length] dimension of both the platform and middle ramp. Along the platform and middle ramp edges, the team plans to install custom-designed sleeve sockets to attach to the handrails’ circular slot ends. So far, our team is leaning on purchasing circular tubes on McMaster to serve as the sockets, however, difficulties arise due to the elevated costs of inner-diameter-based tubes. As we purchase and install the components, we simultaneously consider potential solutions/designs for the sockets.
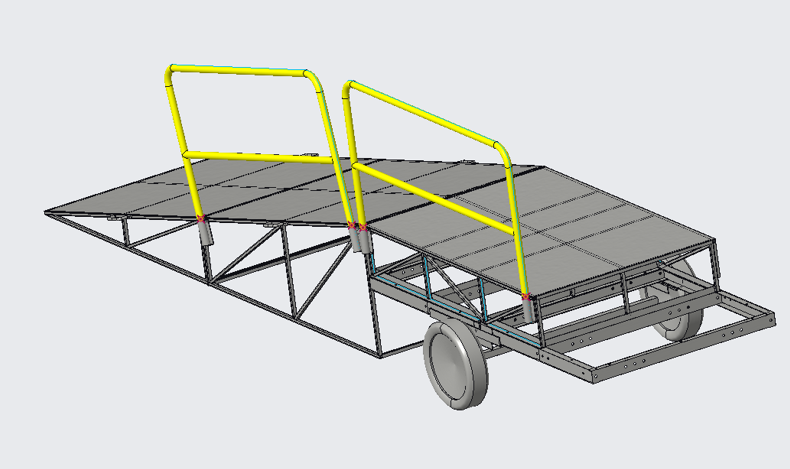
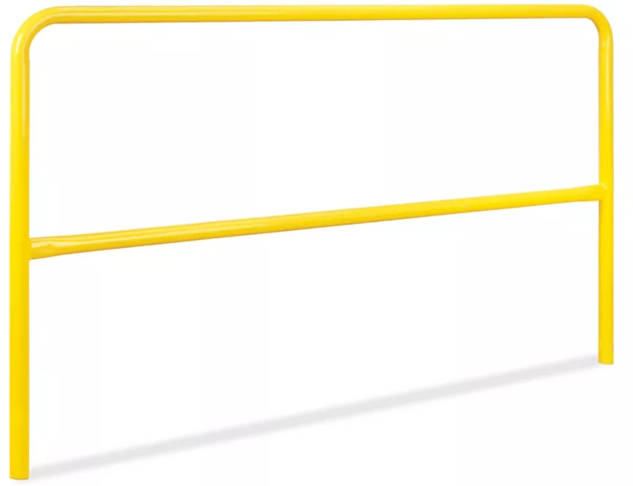
Initially, the team planned to purchase a piano hinge that spans along the width of the mounting ramp. However, this option leads to unnecessarily large costs and excessiveness. Thus, we decided to run with two 1 ft. removable-pin piano hinges attaching to both ends of the platform—middle-ramp joint by welding. A load rating isn’t provided by the McMaster website, thus we gauged a shear strength rating of the hinge pin by performing calculations.
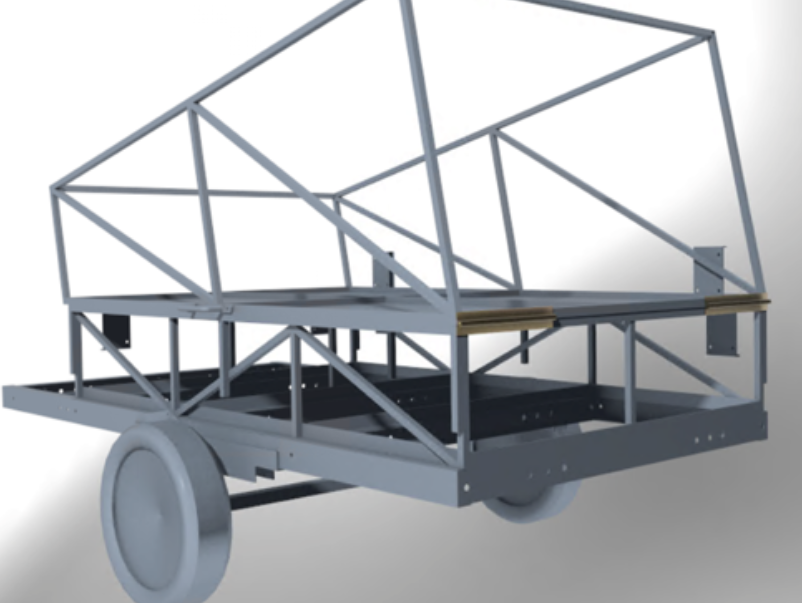
In addition to these main components, we decided to also include several miscellaneous additions. Firstly, we looked into implementing rubber stoppers on the mounting ramp’s front corners to absorb shock in case the middle ramp suddenly drops during the folding process. Websites like McMaster provide stoppers with threaded ends, which we are currently considering purchasing. Additionally, we plan to install an edge-protecting lip along the mounting edge of the platform. With this, we will use a long, flat metal plate to weld across this end.
As described in the previous section, we were considering installing an expanded mounting edge to prevent horses from tripping over the wheels and the side frame tubing. However, the team decided not to go with this idea due to the project partner agreeing to the terms of the previous team’s final design (which didn’t include this feature).
Going into next month, we plan to quickly make our final purchases and begin machining/installing the mounting ramp components. During the month of March, all team members acquired the basic machine shop certification, so we can assist Andrew Bittner during this final assembly process. As of March 31st, 2022, we’ve completed installing the ramp’s trailer rear lights, removed the trailer wheel fenders, and purchased most of the components.
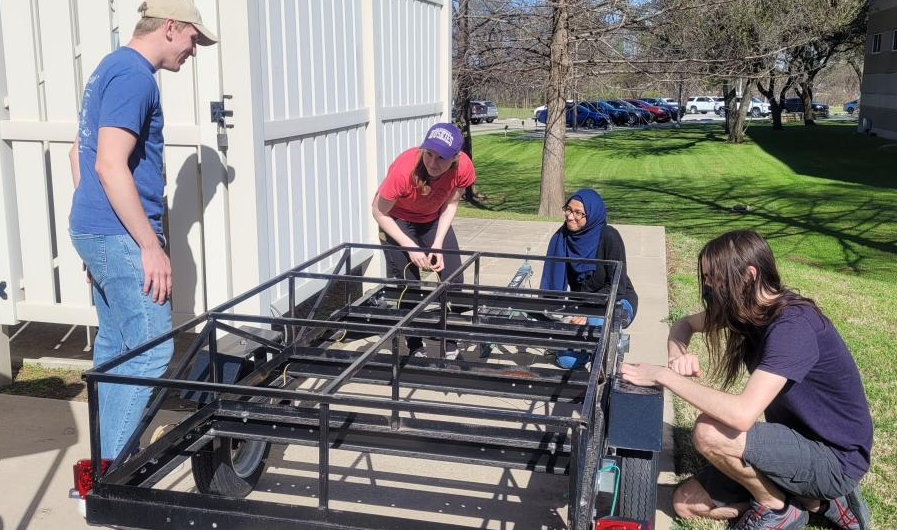