This month, we spent the rest of our time on the project getting the top platform assembled and attached to the trailer base. Aside from that, we spent some time arranging a document for the incoming team that should serve as a crash course into the assembly process and allow them to get started immediately.
Preparation
We began this month by moving the trailer base to the UTD Machine Shop from the UTDesign studio. During this process, we learned that the trailer base is much heavier than we expected – around 500 pounds – which might be an issue further along in the project.
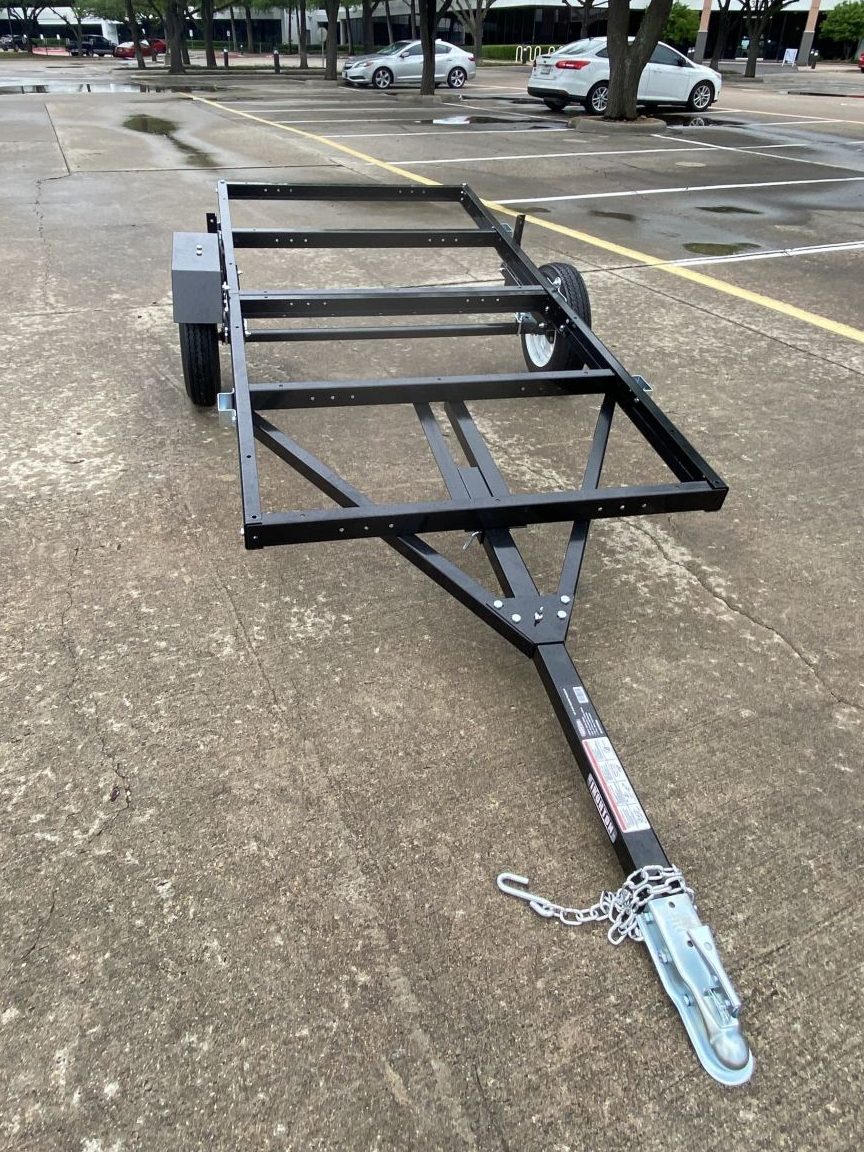
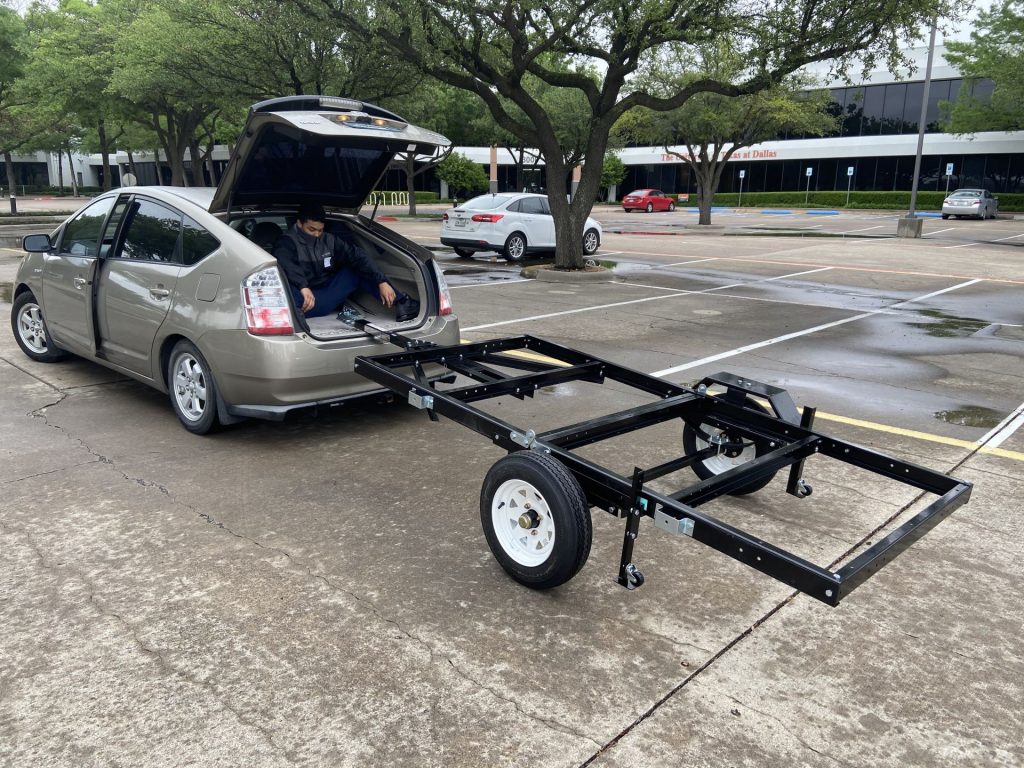
Then, we finished sanding the remaining rough edges on the steel and organized/stored the pieces by length for easy access.
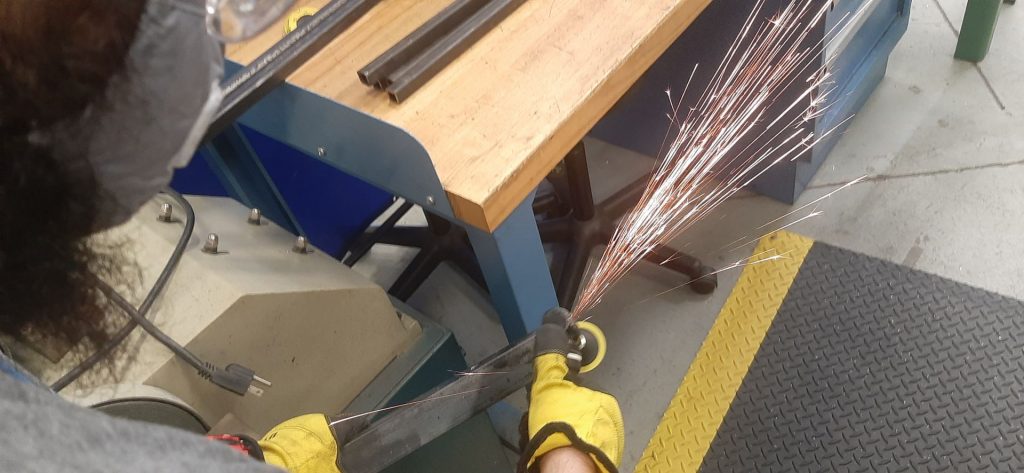
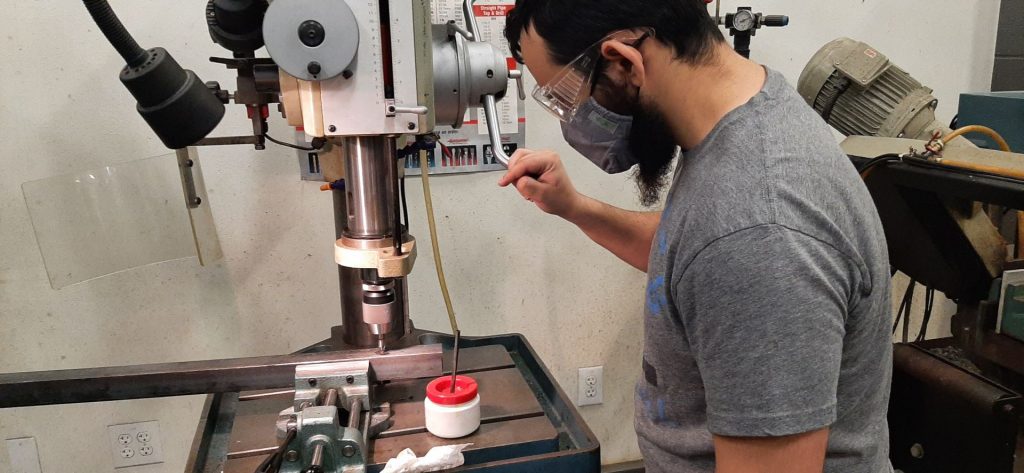
Next, we ordered the nuts, bolts, washers, and Rustoleum that were necessary to successfully complete the attachment of the top platform to the trailer base. In our design, we planned for the attachment between trailer base and top platform of ramp to be through bolting as opposed to welding due to maintenance and trailer replacement considerations. Overall, bolting makes the design much more robust and maintainable for Equest.
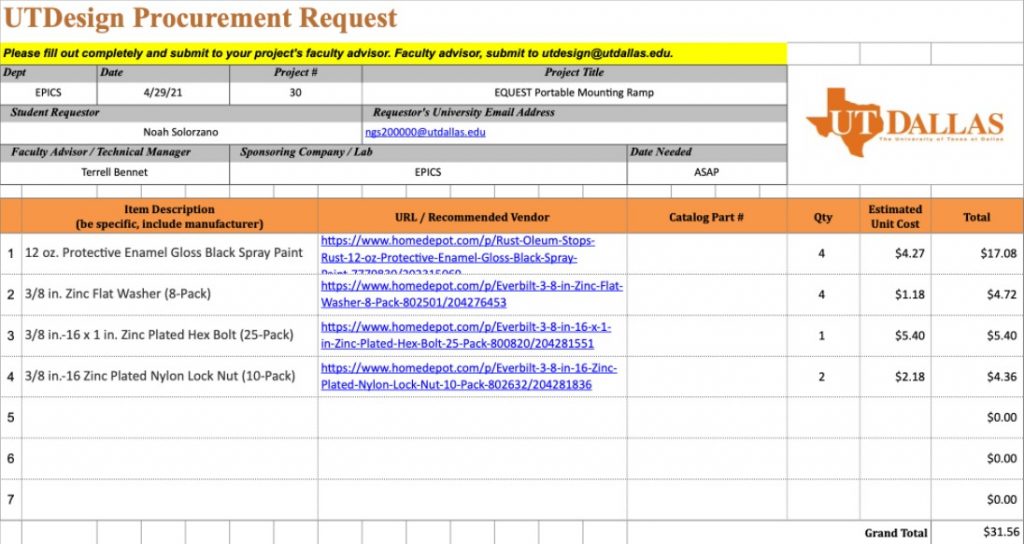
Assembling the Frame
After making preparations, we assisted Andrew Bittner in the UTD Machine Shop with welding. Although we were not allowed to directly weld anything ourselves, we were able to optimize the process through live explanation and smaller tasks.
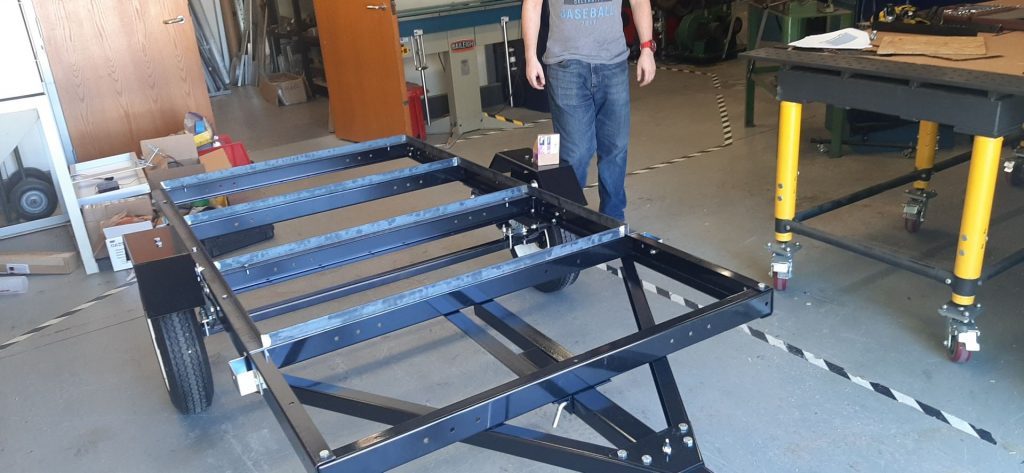
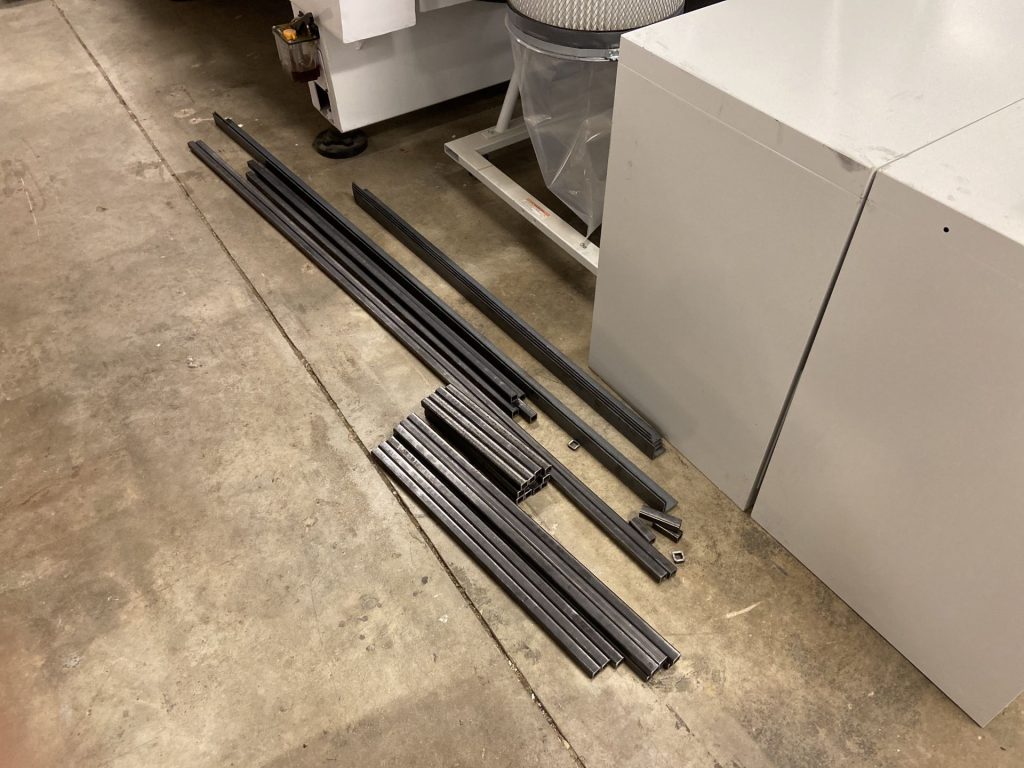
Our final task this semester was to apply a coat Rustoleum to the Top Platform of the ramp to both prevent rust and give it a nicer appearance. As the ramp will likely be stored outside of the machine shop this summer, this was an important step in preserving the structural integrity of the ramp.
Final Message
We spent our remaining free time arranging a document outlining the procedures we took to access the machine shop and to order our materials. Using the Parts List and the Future Procurement Summary, next semester’s team should be able to quickly update the ramp design and begin ordering core components immediately. We wish them the best of luck, and hope to see the Portable Mounting Ramp finally be completed by the end of next semester! Neigh Sayers, signing off.