This month, we focused on the logistics of the ramp and we are now ready to order components for assembly in April. Concerns this month included: trailer base modelling, machinist consultation, design optimization, and price quote comparison.
Firstly, we contacted Andrew Bittner from the UTD Machine Shop to discuss the feasibility of machining our current platform design and our idea to cut excess length off of the trailer base. From this meeting, we got confirmation and advice on many of our design questions, and quickly went to work amending and updating our designs.
Trailer Base Cut
First, we created a model of the trailer base in CREO in order to simulate the assembly of the top platform of the ramp to the top of the trailer base. This model helped us convey our design concept to Andrew, and allowed us to discuss more specific concerns.
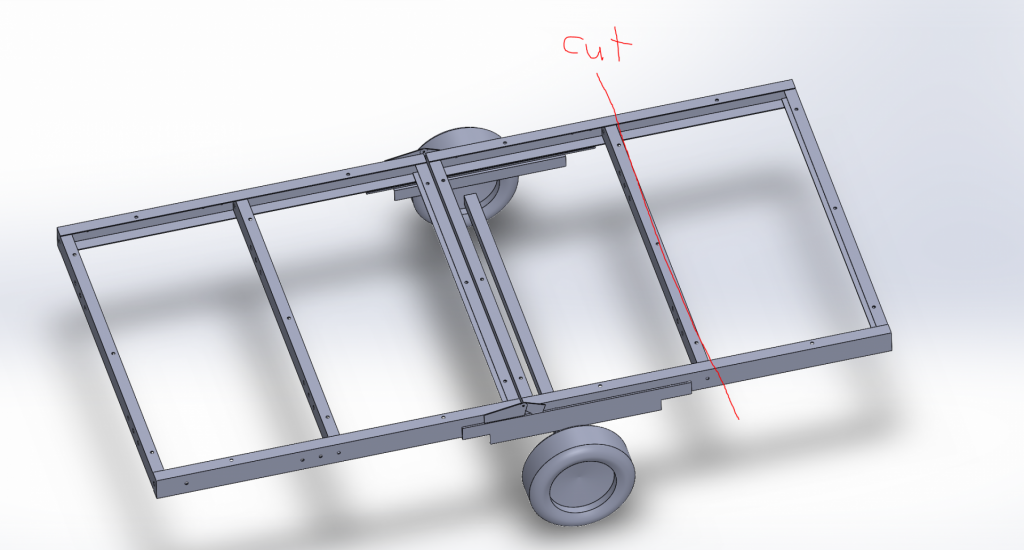
Using the trailer base model, we consulted with Andrew Bittner and our project mentors to determine if a cut on the trailer was appropriate. In the end, we determined that cutting the trailer would result in a potential loss of structural integrity and handling on the road.
Top Platform Mounting Solution
Next, we used the input from Andrew Bittner to determine the optimal way to mount the Top Platform of the ramp to the top of the Trailer Base. Our problem was that the platform design inherited from last semester had 1 set of central mounting legs, while the trailer base has 2 central, horizontal supports at the center that do not align with that of the top platform.
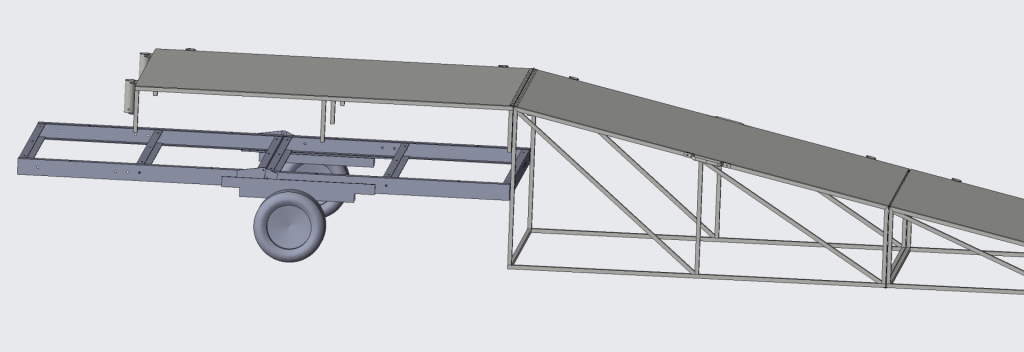
Our solution, approved via email confirmation by Andrew Bittner, was to restructure the central support of the Top Platform into 2 centralized sets of supports that mirror the dimensions of the Trailer Base’s crossbeams.

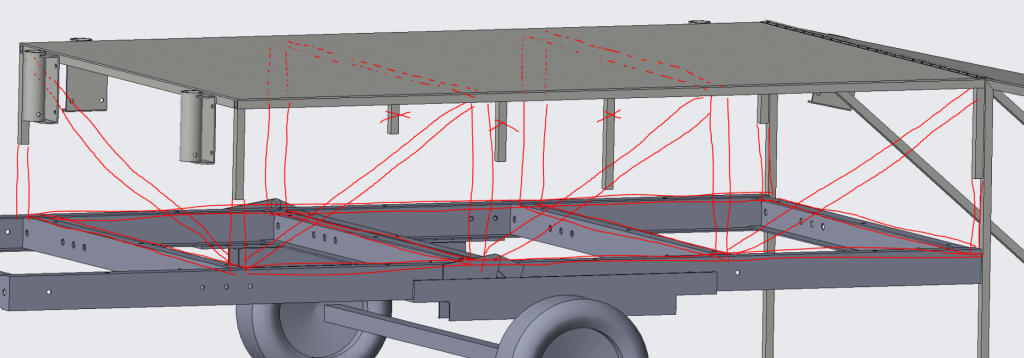
To mount the Top Platform supports to the Trailer Base more effectively, we added angle iron cross beams along the bottom of the supports. After implementing the Top Platform mounting solution to our model, we updated our material procurement lists and reassembled the 3D model of the ramp.
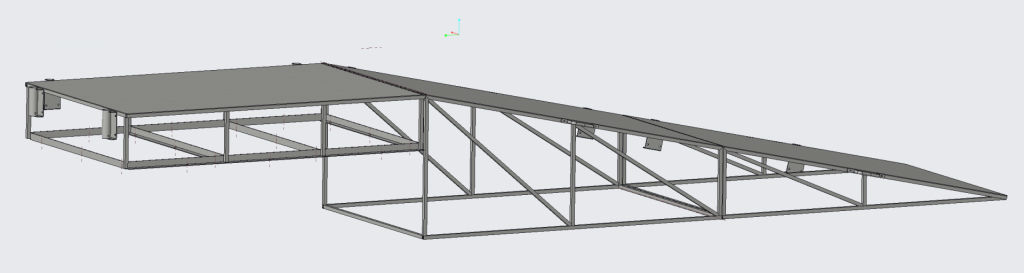
The “Impossible” Tubing Cut
The last major concern for the ramp was a certain cut of steel tubing on the Bottom, or loading, Segment of the ramp that Andrew Bittner told us was impossible to perform due to the angle.
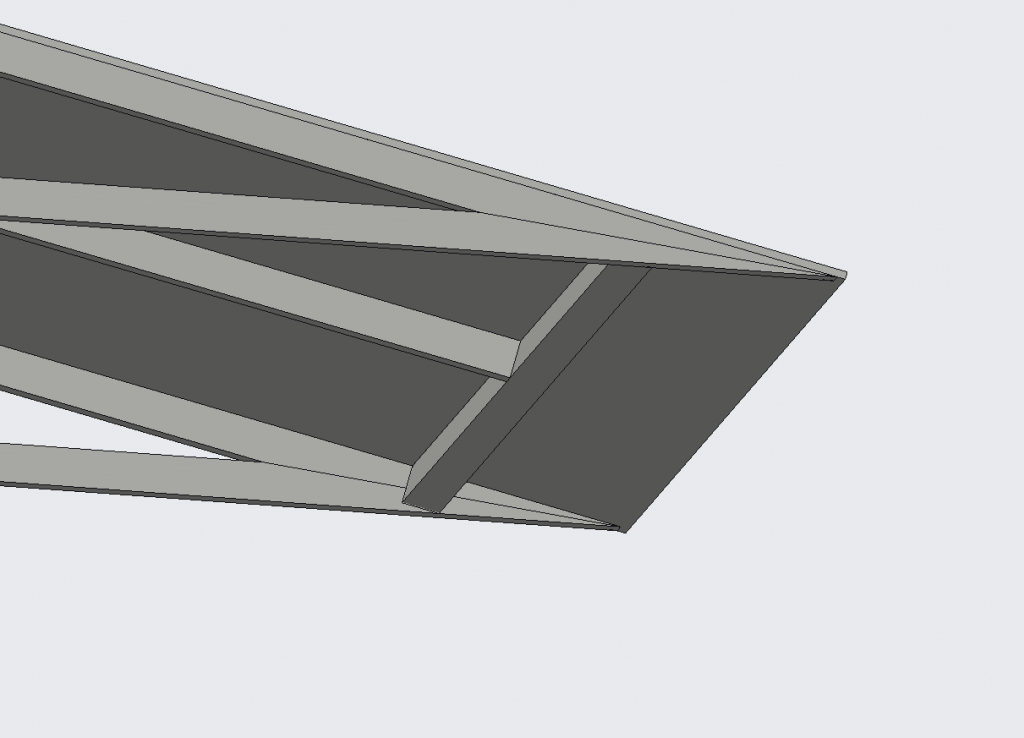
After consulting with our project partner, Bobby Valdez, we were relieved to learn that a small gap between the ground and the lowest point of the ramp of about 2 inches was acceptable. Using this information, we amended the cut on the steel tubing.
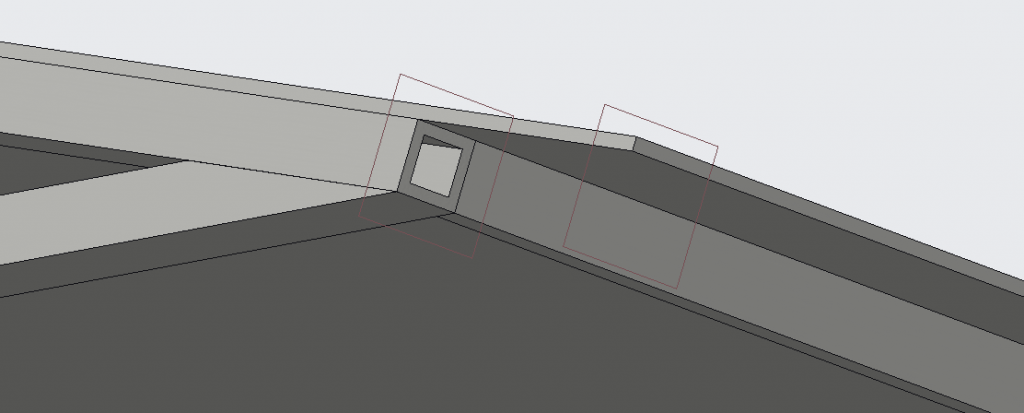
Although the steel tubing cut is now resolved, we are currently discussing the removal of the overhanging portion of the expanded metal resulting from the design change. Because it is the lowest part of the ramp and is now unsupported by steel tubing, we have concerns that the expanded steel may eventually wear away from impacts with the ground. We will consult with Andrew Bittner, Bobby Valdez, and our project mentors to resolve this concern.
Price Quote Comparisons
Our final task this month was to call UTD approved steel vendors and compare purchase prices for the materials we need to complete the Top and Mid segments of the ramp. We are comparing many parameters to determine the best vendors, namely: gross cost, cost per unit, shipping fee, locality, and favor with the university. We will have our procurement form ready for approval in early April.
Plans for Next Month
Next month will be crucial for this project: we will be ordering components and consulting with the UTD Machine Shop a lot. We will also begin work on the design of the Permanent Safety Guard Mounting solution discussed with Andrew Bittner. While we work on this, the Top Platform will be machined, and we will need to coordinate with the UTD Machine Shop and UTDesign Studio to navigate the Trailer Base (currently in the UTDesign Studio) to the machine shop.